For the same exterior loading, the stress produced within the cladding, either external from the coolant or internal from fission-product swelling of the gasoline, is lowered in proportion to the wall thickness. However, thick cladding is detrimental to neutron economic system, increases the quantity of the reactor core, raises gas temperature, and costs more than skinny-walled tubing.
The Building Research Establishment (BRE) has been commissioned to undertake this project. This programme is on-going and tests are expected to conclude in the summertime.
Hydrogen addition in boiling water circumstances just isn't very effective because of the segregation of hydrogen in the steam part. The interplay that fuel cladding tubes experience because of the fission products on the inner surface is stress corrosion cracking (SCC). Iodine, caesium, and cadmium are some of the fission merchandise which contribute strongly to the SCC process. Due to the combined results of thermal expansion of gasoline pellets, gasoline swelling because of fission fuel release, and the coolant stress on the outer surface of fuel tubes, cladding tubes collapse on the gasoline pellets.
The low burnup habits is managed by elements such as pellet densification and gasoline-clad hole closure, but at larger burnups conductivity degradation turns into more and more vital, driving the temperatures up to and past the extent the place gaseous and unstable fission products begin to be released from the fuel. The consequences of this are thought-about additional in later sections. because of their corrosion resistance to acids and bases and their low neutron-absorption charges. Zircaloys have anisotropic physical, mechanical, and chemical properties. Within the oxide layer, the alloying components affect the atomic transport such that the alloying concentration determines the corrosive conduct, with excessive alloying concentrations (above ∼zero.6%) providing safety in opposition to oxide growth.
The thickness of the cladding may range between zero.1 and 30 mm and the detonation velocity is between 1200 and 7000 ms −1 . The high plate hits the underside plate with a velocity of 100–a thousand ms −1 , and pressures are in the range of 10 to one hundred kbar. Under sure conditions a superheated layer of fabric types within the contact space. The joint is then attributable to a deformation-induced melting bathtub.
The compromise between these competing demands has produced wall thicknesses of ∼0.9mm in BWRs and ∼0.7mm in PWRs. Laser cladding usually entails masking a comparatively inexpensive substrate material with a dearer alloy that may enhance the resistance of the part to wear or corrosion.
is produced and the chance of a large secondary hydriding failure is elevated. In response to this unexpected consequence, several fixes have been launched.
The buildup of those could be suppressed by including hydrogen in the coolant water. Dissolved hydrogen focus in PWR coolant is maintained at a level of 2.2–4.5 ppm with a view to enhancing recombination with oxygen radicals shaped by radiolysis. The PHWR coolant doesn't include boric acid and deuterium is added rather than hydrogen.
Enhance the curb enchantment of your home with B&Q cladding. All of our timber is responsibly sourced forest pleasant timber.
Alloying parts, notably tin, niobium, and iron, current in the α-solid resolution strongly influence each the kinetics and the mechanism of oxide progress in zirconium alloys. ions from the setting to the reaction front at the metal/oxide boundary.
This is a main cladding failure that admits steam into the rod with the accompanying potential for a more severe secondary failure as a result of hydriding. The mixture of conditions (vulnerable steel, tensile stress, and chemical enhancer) that produces the first defect is termed pellet–cladding interaction (PCI). scale that grows round them during in-reactor operation. This loss of the insulating properties of the oxide is believed to accelerate the corrosion rate.

Fast Breeder Reactors: reference Fuels
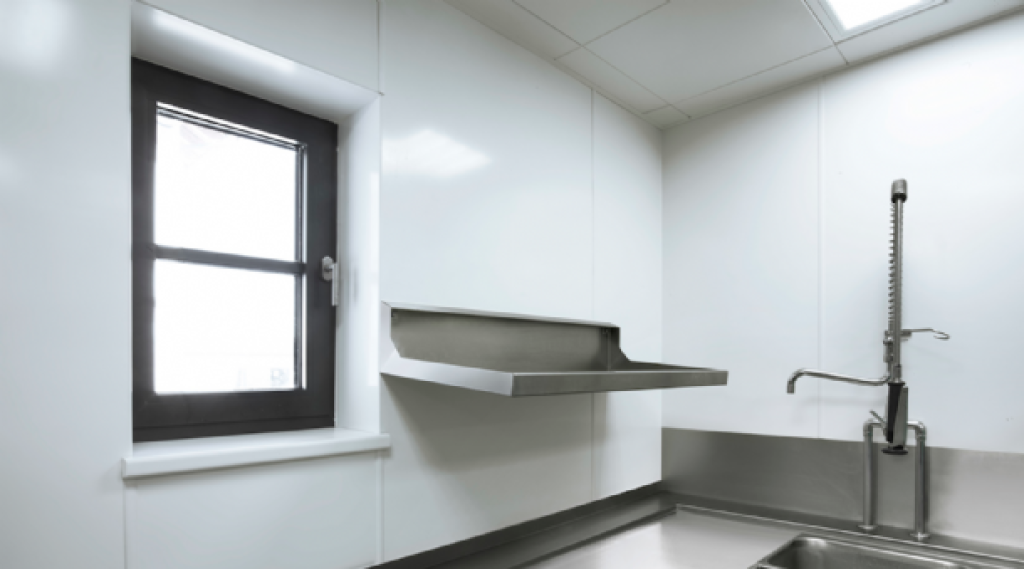
The low burnup behavior is managed by components similar to pellet densification and gas-clad hole closure, however at higher burnups conductivity degradation becomes increasingly important, driving the temperatures as much as and past the extent where gaseous and risky fission merchandise start to be released from the gas. The consequences of this are thought of additional in later sections. due to their corrosion resistance to acids and bases and their low neutron-absorption charges. Zircaloys have anisotropic bodily, mechanical, and chemical properties. Within the oxide layer, the alloying elements influence the atomic transport such that the alloying focus determines the corrosive behavior, with high alloying concentrations (above ∼0.6%) providing protection in opposition to oxide development.
The thickness of the cladding may vary between 0.1 and 30 mm and the detonation velocity is between 1200 and 7000 ms −1 . The top plate hits the underside plate with a speed of a hundred–1000 ms −1 , and pressures are within the range of 10 to 100 kbar. Under certain circumstances a superheated layer of material varieties within the contact space. The joint is then brought on by a deformation-induced melting tub.
Zry production strategies now offer much better control of gaseous impurities than early fabrication expertise, so the unique cause for including tin is moot. Since tin is a substitutional impurity, its function is to increase the strength of Zry over that of pure zirconium. 1.5% tin, and the balance being iron, nickel, and chromium.
The full melting of the filler leads to a dense layer with optimum adhesion to the substrate. The most typical application is for the wear and tear protection, e.g. of instruments, but in addition corrosion protection or excessive temperature resistance may be particularly improved. Common exhausting alloys primarily based on cobalt, nickel and iron are used with and without the addition of hard supplies. But also specifically adapted materials can be utilized.
The graphite layer offers lubrication to reduce the mechanical interactions, and acts as a barrier towards the migration of dangerous species to stressed areas of gasoline tubes. The authentic purpose of tin in Zry was to mitigate the lack of corrosion resistance attributable to pickup of impurity nitrogen throughout fabrication of the alloy.
Alloying parts, particularly tin, niobium, and iron, current in the α-strong resolution strongly influence each the kinetics and the mechanism of oxide progress in zirconium alloys. ions from the surroundings to the reaction entrance at the steel/oxide boundary.
These approaches have encountered problems, together with porosity of the cladding, uneven cladding thickness, dilution of the cladding alloy because of the massive heat input required, and distortion of the workpiece by the excessive heat enter. Laser cladding has lowered these problems and produced cladding layers with good uniformity, good dimensional control, and minimal dilution of the cladding alloy. provides a survey of a cladding tools. If the incoming strips have to be heated to be able to decrease the strength of materials, this needs to be done as shut as possible to the rolling gap and in a protecting ambiance in order to avoid oxidation of the cleaned and roughened surfaces. We provide excessive-high quality ornamental products that enhance any house and interior.
D. Cheapest Cladding MaterialCost Of Timber Cladding Laser Cladding
For the identical exterior loading, the stress produced within the cladding, either external from the coolant or inner from fission-product swelling of the fuel, is lowered in proportion to the wall thickness. However, thick cladding is detrimental to neutron economy, increases the amount of the reactor core, raises gas temperature, and costs more than skinny-walled tubing.
The buildup of these may be suppressed by adding hydrogen within the coolant water. Dissolved hydrogen focus in PWR coolant is maintained at a stage of two.2–four.5 ppm with a view to enhancing recombination with oxygen radicals formed by radiolysis. The PHWR coolant does not comprise boric acid and deuterium is added in place of hydrogen.
The low burnup behavior is managed by factors corresponding to pellet densification and fuel-clad gap closure, however at greater burnups conductivity degradation turns into more and more significant, driving the temperatures up to and past the level the place gaseous and volatile fission products start to be launched from the gasoline. The consequences of this are considered further in later sections. because of their corrosion resistance to acids and bases and their low neutron-absorption charges. Zircaloys have anisotropic bodily, mechanical, and chemical properties. Within the oxide layer, the alloying elements affect the atomic transport such that the alloying concentration determines the corrosive conduct, with high alloying concentrations (above ∼zero.6%) providing protection against oxide development.
In addition to metallurgical factors, water chemistry has a robust affect on the corrosion course of in zirconium alloys. The management of water chemistry as required in numerous reactor techniques embody suitable additions of lithium hydroxide, boric acid, hydrogen/deuterium, oxygen, iron, and zinc. In PWRs, boric acid is added to the coolant water for reactivity control. The pH of the coolant is adjusted by addition of lithium hydroxide which renders the coolant slightly alkaline, to be able to scale back the corrosion charges of structural supplies (stainless steels and Inconels) in the main heat transport circuit and thereby inhibit deposition of corrosion merchandise on the gasoline cladding. Radiolysis of water produces oxidizing species which boosts oxidation price of zirconium alloys in the radiation surroundings .
Dissolved oxygen in PHWR coolant is managed between 10–50 ppb and it has been observed that corrosion in each zircaloy-2 and Zr-2.5 Nb pressure tubes rises to an exceptionally excessive value at high oxygen concentrations. The BWR coolant usually contains a better level of oxygen, usually 200–400 ppb.

Metallverkleidung f

tube. Energy, from fission, is generated roughly uniformly all through the fuel pellets. Heat is extracted at the rod floor by the coolant flow. The temperature on the hottest level, at the pellet centerline, is typically in the range 800–one thousand °C, relying on the power degree. The metallic cladding is a good conductor, so the temperature rise throughout the wall is just a few tens of degrees.
This method is adopted for zircaloy-clad fuels from power reactors and chrome steel-clad quick reactor fuels. Like the cladding , under the impact of neutron flux the hexagonal wrapper tube undergoes change. Geometrical changes, induced by swelling and irradiation creep (underneath the impact of dynamic sodium strain), concern length, across-flat dimension, and, for subassemblies placed within the periphery of the core, bowing (differential swelling induced by differential flux and temperature between opposite faces of the wrapper tube).
As a remedy, speedy cooling of the Zry ingot during fabrication (referred to as beta quenching) produces a much finer intermetallic precipitate inhabitants. This distribution of the transition metals maintains the power of the Zry but improves its corrosion resistance, presumably by quick-circuiting charge-transport paths between the scale surface and the metal–oxide interface. In order to eliminate waterside corrosion of cladding as a life-limiting process, modified Zircaloys have been developed. Under PWR water situations, lowering the tin content of Zry to 1% and including a comparable focus of niobium produces an alloy with a corrosion fee a number of occasions decrease than that of the standard Zry. Modified low-tin alloys can be utilized both as a whole substitute for the Zry tube wall or as a skinny outer pores and skin on commonplace Zry substrate tubing.
Depending on the supplies to be bonded, cleansing and roughening are best carried out by brushing, grinding, or scraping utilizing a specially designed cutter with needles. A suction elimination unit is used to evacuate carefully any material waste to be able to avoid bonding flaws on account of poor adhesion. Laser cladding allows us to use steel layers for put on and corrosion safety with nice precision. In addition, it can be used to repair and modify components.
The low burnup habits is managed by elements similar to pellet densification and gasoline-clad hole closure, but at higher burnups conductivity degradation becomes increasingly vital, driving the temperatures as much as and beyond the level the place gaseous and unstable fission products begin to be launched from the gasoline. The penalties of this are thought-about further in later sections. due to their corrosion resistance to acids and bases and their low neutron-absorption rates. Zircaloys have anisotropic physical, mechanical, and chemical properties. Within the oxide layer, the alloying elements affect the atomic transport such that the alloying focus determines the corrosive habits, with high alloying concentrations (above ∼0.6%) providing protection in opposition to oxide development.
In one, a second inner-surface liner of ordinary Zry is extruded on the sponge zirconium liner to be able to restore corrosion resistance. In different modifications, the sponge zirconium is alloyed with iron or tin to improve oxidation resistance without affecting the softness that gives immunity from PCI. Standard Zry is sufficiently exhausting to be prone to stress-corrosion cracking (SCC) when the pellet–cladding hole closes and the swelling gasoline generates substantial tensile hoop stresses in the cladding. In the presence of an aggressive fission product (iodine is most often cited), a brittle crack may be initiated and penetrate the cladding wall.